麻烦哪位大哥大姐帮我翻译下这段科技文The material removal mechanism of WEDM is very similar to the conventional EDM process involving the erosion effect produced by the electrical discharges (sparks). In WEDM, material is eroded from
来源:学生作业帮助网 编辑:作业帮 时间:2024/11/29 06:36:16
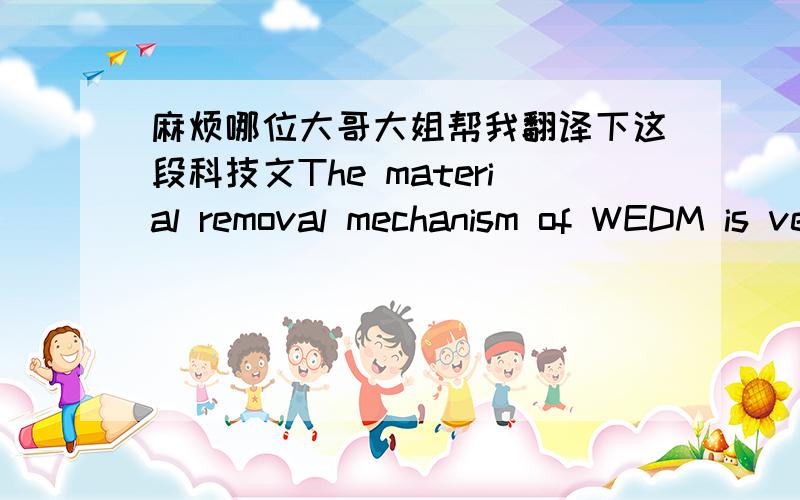
xWRW~428$SJTS3SJ*Muխt I&d1w1,$.sZ}N}^{7spdϽ g+>~ZUޓ6ռ\1Y0-5uKsY,32mzYIk?|ſ5;yfִtWǛc07oѹ4pǘx8t>J
)n?;^Nwyw?l "qp3i>sW8AQd ?t4Os#7^zbx%ܚ.ӳ2hZK[y33!`7!-7#1mgfZǽIgΤKM#f0ن!k:[8P`u6-M?s{R>zNjYgTu|es|_3-ө54LzJy9f Fh!0R1G6OjkdGa
|H (FE'sek7tJQ[Sσބ~ȪvnꊞjD5.L~Ӯs
||ҫ9,3f~ji/>h2= 6=Ҡ<(ERBp
/uC1i9bILx.oy*N
G;R;Prs9TvDo~zK"%HtBݡ+ЇA祜AjJ$4BpIHB>`%y+Nຒlr"}݀AХ2U?:߾iX Ӷ",fы?k03sM5-9"R2TfZ:oE ϓmLBI%=c+Ǻa?,s|CF)qccއ.Osd9Zl+'"J$!JjovLJG Wv='hD3@uC]٬r죮;JaA'a9}.aE`Qm@ZoSOݯ
"=#b 1oӌԕs7*Pw[(6A$7;u*r9_2Gce?I=ƅ Ԫ,F6|ّͅbyr*CTFm;Urf$4İ"UGYN -'jOКp]!ST*Ɯ2fbH)ڝA?R